Streamline Materials Receiving to Improve Inventory Control
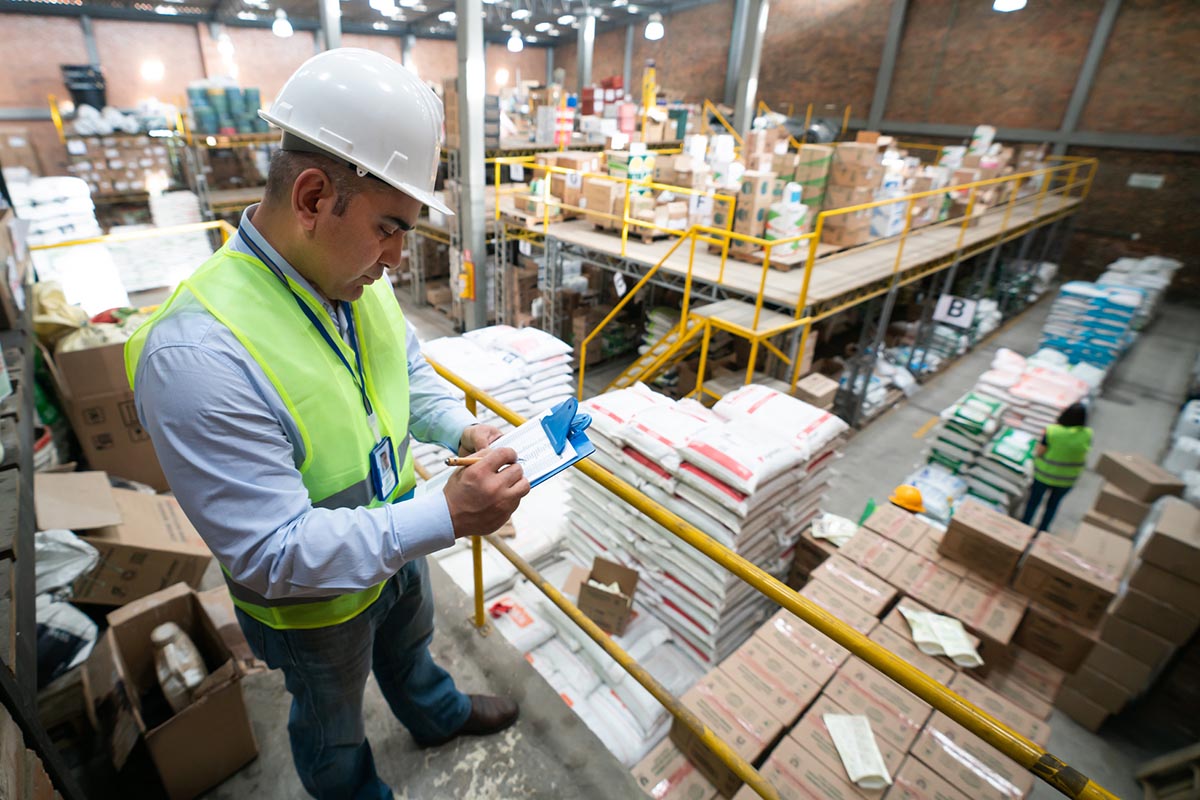
With all that goes into the construction planning procurement process, identifying areas for improvement can be challenging. Construction managers require a reliable way to ensure they’re making informed decisions throughout every step of the overall process and optimizing operations at every checkpoint—one of which is receiving materials at the jobsite.
Efficient materials receiving demonstrates the importance of accurate delivery logs to the jobsite and warehouse for tracking inventory, delivery issues, and historical records of purchase order fulfillment. This step of the construction plan can prove particularly complex, especially when dealing with large volumes of materials. Refining this process helps to avoid issues further on in procurement by promptly relaying data back and forth for streamlined management and recordkeeping.
When was the last time you took a close look at your materials receiving protocol? An audit of this workflow can reveal decentralized or fractured processes and uncover inefficiencies that might be causing unnecessary losses. We can start by addressing the functionalities involved in materials receiving and what it looks like to optimize this process.
Weaknesses in Materials Receiving
Believe it or not, up to 30 percent of all building materials delivered to a typical construction site wind up as waste. But a digitized materials receiving system can help to alleviate this common problem and other pain points in construction planning.
When it comes to enhancing materials receiving, first perform a self-audit, addressing the weak spots in your strategy and finding the best ways to improve upon them. Below, we pose three crucial questions that can help to identify the parts of your materials receiving process that may need attention.
How are you tracking deliveries in the field?
Manual processes such as paper logbooks lack transparency and convenience, plus they often lead to miscommunication and disputes with vendors. When jobsite crews don’t know where materials are, they’ll spend more time looking for supplies and less time tending to their job requirements. When materials can’t be tracked down on-site when they’re needed, the resulting discrepancies lead to duplicate orders and major cost overruns.
What’s going on with deliveries to the warehouse?
Materials received at the warehouse come from several sources, including both vendors and the crew in the field. Improper or inconsistent logging and tracking of inventory can have significant accounting implications. If the warehouse doesn’t accurately manage job materials and general stock, for example, needless procurement and inventory expenses tend to quickly stack up.
How are your delivery receipts logged?
Using paper delivery receipts to document delivery confirmations can cause issues for the following reasons:
- They’re easily lost or misplaced before they make it to the office.
- They require manual review and data entry.
- They’re not always a reliable, complete record of the delivery.
- They won’t reflect damaged materials.
- They require time-consuming accounting follow-ups.
- They’re not always legible if they’re handwritten.
With the right strategy and capable software, all of these inefficiencies can be identified and addressed with ease.
Strengths of Digital Receiving Systems
Adequate construction management becomes a lot simpler when you implement a digital system that automates repetitive receiving tasks, such as logging, tracking, and managing inventory. Great systems for materials receiving can provide the following advantages for construction planners:
- Gain visibility into warehouse needs.
- Lower costs and expenses.
- Reduce project waste.
- Anticipate potential risks.
These benefits are attributed to streamlined processes for organizing delivery and inventory data, which saves time and stress for everyone involved. The following additional functionalities of digital receiving systems work in tandem to refine this stage of procurement:
Digital Delivery and Material Tracking in the Field
Implementing a digital receiving system saves time and creates a comprehensive, easily accessible record of all deliveries and related details. Through this software, field teams can quickly and accurately log deliveries and note any issues, such as damaged or missing materials. On the other end, the office team can receive up-to-date delivery information instantly, which allows for timely processing of invoices and payments.
Digital Inventory Management in the Warehouse
The right software solution also allows warehouse managers to properly log materials and easily share inventory data with other teams, providing transparency and enabling better coordination. Accurate inventory data means that purchasing teams can make informed decisions about future orders. This initiative helps to reduce the risk of overstock or stockouts and ensures timely delivery of materials.
Keep Construction Planning Projects on Track
By using digital systems to fill in the gaps in construction planning, you can optimize inventory management and materials receiving, resulting in a much smoother procurement process overall. When construction planners seek to better this process, it’s crucial that they consider each of the seven steps to better procurement for specialty contractors:
- Materials planning
- Materials sourcing
- Materials purchasing
- Materials requesting
- Materials receiving (here)
- Invoice matching
- Materials payments
You don’t have to alter your whole business plan to get procurement on the right path. By offering the right software, technical support, and industry expertise, Kojo provides you with everything you need to build a quality construction management plan that prioritizes efficiency across all aspects of your business. Learn more through through the 7 Steps to Better Procurement for Specialty Contractors.
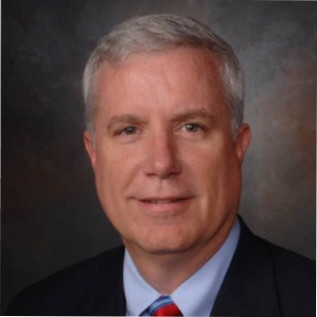